Semeadora mecânica e pneumática: confira as vantagens, desvantagens e recomendações para o uso em sua propriedade
O processo de semeadura é uma das etapas mais importantes na formação de cultivos agrícolas. Ele impacta na taxa de germinação de sementes, na população inicial e no vigor de plântulas, além de influenciar muito nos resultados de produtividade.
Existem dois tipos básicos de maquinários para semeadura que normalmente são utilizados na atualidade: as semeadoras mecânicas e as pneumáticas.
Ambas apresentam vantagens e desvantagens e podem ser indicadas de acordo com as características da área e da propriedade.
Neste artigo, você verá as principais diferenças técnicas entre as duas opções de semeadoras, suas recomendações, custos e impactos na formação da lavoura. Confira!
Qual a importância da semeadura na atividade agrícola?
A semeadura é uma atividade inicial do processo de produção agrícola, essencial para a definição da produção potencial ao final do ciclo de cultivo.
É durante a semeadura que se define:
- o estande inicial;
- a distância entre plantas e linhas de semeadura;
- a população total por área.
Isso definirá o grau de competição entre plantas por luz, nutrientes e água, podendo potencializar a produção de biomassa, quando feito de maneira correta.
Além da necessidade de entregar sementes em quantidade e espaçamento ideal, condições ótimas para a germinação de sementes são criadas através da profundidade de semeadura, aumentando a taxa de germinação e o vigor de plântulas.
O que interfere na qualidade da semeadura?
A semeadura, junto aos processos e insumos utilizados nela, é responsável por grande parte dos custos de produção de um cultivo, desde o preparo do solo até a colheita.
Esses valores podem variar de acordo com a cultura, mas estão entre 40% e 50% do custo total de produção em grãos.
Esse fato aumenta a necessidade de uma semeadura de qualidade e com o mínimo de falhas possíveis.
Dentre os fatores que mais afetam a qualidade da semeadura, podemos listar os seguintes:
- semente: a qualidade da semente deve ser julgada não só por seu potencial de germinação e pelas suas características fisiológicas. É importante ressaltar a homogeneidade de características físicas e morfológicas como tamanho e forma, o que pode impactar no desempenho das semeadoras;
- semeadora: a escolha da semeadora acontece em função da cultura, do tipo de plantio e das características do solo. Algumas atividades executadas pela máquina semeadora são: corte de palhada, abertura de sulco, distribuição e cobertura de sementes e disposição de fertilizantes;
- solo: a cobertura do solo, sua umidade e características físicas como granulometria, estrutura, densidade, constituição e topografia podem alterar a qualidade de semeadura e interferir na decisão do maquinário.
Diferenças entre semeadoras mecânicas e pneumáticas
Ao longo do tempo, muitas foram as formas utilizadas por agricultores para a execução da semeadura. Atualmente, as principais opções para semeadoras são as mecânicas e as pneumáticas.
As semeadoras mecânicas funcionam com base na distribuição de sementes por meio da gravidade. Essas sementes são colocadas em discos que podem ser dispostos na direção vertical, horizontal e inclinada.
Já as semeadoras pneumáticas são mais modernas e funcionam com base na distribuição de sementes através de vácuo. As sementes são retidas em furos pela pressão negativa gerada.
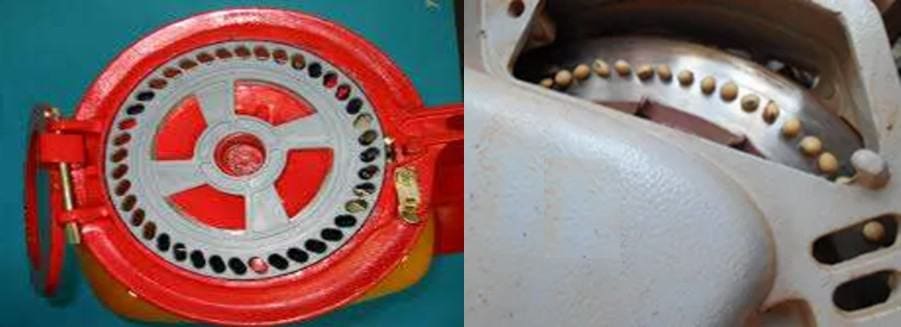
Sistemas de distribuição de sementes em semeadoras mecânicas (esquerda) e pneumática (direita)
(Fonte: Mais Soja, 2018)
Hoje em dia, nas propriedades brasileiras, 70% das semeadoras são mecânicas. Porém, a maior disponibilidade de semeadoras pneumáticas, em conjunto com preços mais acessíveis, deve gerar uma igualdade, em porcentagem, em um futuro próximo.
Vantagens e desvantagens dos dois sistemas
Podemos comparar as semeadoras mecânica e pneumática usando vários parâmetros. A seguir, mostramos alguns dos mais importantes:
Custo
As semeadoras mecânicas são, em geral, mais baratas que as pneumáticas. São mais acessíveis para produtores com menores áreas ou investimentos, também por apresentar menor depreciação.
Já as pneumáticas são mais caras em preço de aquisição e manutenção e, pela tecnologia envolvida, têm maior depreciação.
Tecnologia
As semeadoras pneumáticas apresentam um grau de tecnologia maior que as mecânicas. Isso se dá pela presença de um sistema mais moderno de controle de distribuição da semente.
Operação
As semeadoras mecânicas necessitam de ajuste e adequação de discos dependendo do tipo da cultura a ser semeada. Isso demanda um maior cuidado e gasto de tempo na operação.
A semeadora pneumática, por sua vez, tem menor necessidade de ajustes durante a operação, pois o sistema de vácuo se adequa a diversos tamanhos e tipos de semente.
Energia
As semeadoras pneumáticas precisam, normalmente, de tratores de maior potência e apresentam maior gasto de energia pela presença da turbina de vácuo.
As mecânicas são mais robustas e necessitam de menor energia para a operação.
Qualidade
Ambos os tipos são capazes de executar a semeadura com alta qualidade quando bem reguladas e operadas. Porém, com a semeadora mecânica, há uma maior chance de dano mecânico na semente ao passar pelo sistema de discos.
Rendimento
Em termos de rendimento, a semeadora pneumática tende a cobrir uma área maior que a mecânica no mesmo tempo de trabalho. Isso porque a velocidade recomendada para as semeadoras pneumáticas é cerca de 2 km/h a mais que para as mecânicas.
Modelos de semeadoras mais usadas no país
Os maquinários agrícolas para semeadura são normalmente disponibilizados nos tipos de distribuição, mecânico ou pneumático.
Além disso existem múltiplas opções como semeadoras para plantio convencional ou plantio direto, com ou sem adubadora, de acordo com o número de linhas, para sementes graúdas (milho, soja, algodão, feijão, sorgo e girassol) ou sementes finas (trigo, aveia, arroz, cevada e canola).
Aqui destacamos as marcas e modelos mais utilizados para plantio direto de sementes graúdas no Brasil.
Uma das marcas de maior uso no mercado nacional é a Tatu Marchesan, com os modelos mais comuns sendo o PST4 (mecânica) e o PST4 Suprema (pneumática).
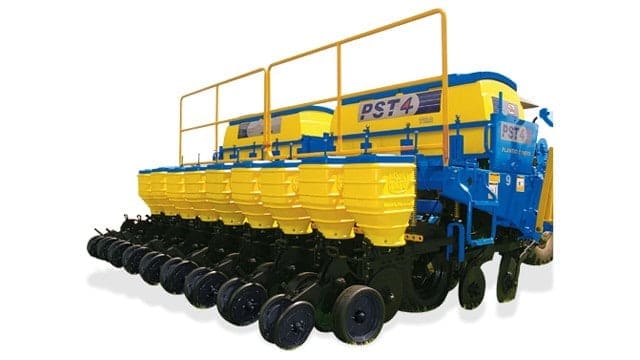
(Fonte: Tatu Marchesan)
Outra opção é a marca Jumil, sendo os modelos Exacta Air JM 8090 (pneumática) ou Magnum JM 8080 (mecânica) as mais comumente utilizadas.
Outras marcas são a John Deere em que a Série 1113 apresenta opções mecânica e pneumática para um número menor de linhas ou a série DB para maior número de linhas.
Outra marca disponível é a Stara com a linha Prima (mecânica) e Victória (pneumática).
Além disso, existem outras opções como a Massey Ferguson com os tipos MF 512 MM (mecânica) e XH (pneumática), por exemplo.
Uma opção adicional é a marca New Holland com a linha Sol Tower com as duas opções, mecânica e pneumática.
Conclusão
A semeadura é responsável por grande parte dos custos de produção de um ciclo de cultura. Sua qualidade é dependente de fatores como a escolha da máquina semeadora mais adequada, sendo que, atualmente, as mais usadas são as mecânicas e pneumáticas.
Essas semeadoras apresentam modos de funcionamento diferentes, assim como múltiplas vantagens e desvantagens, como vimos ao longo do texto.
A escolha da semeadora deve ser feita de acordo com o tamanho da área, nível tecnológico e capacidade financeira do produtor.
Para áreas maiores e com altas demandas tecnológicas, as semeadoras pneumáticas podem ser mais efetivas devido à maior velocidade de operação e menor necessidade de manutenção.
Já as semeadoras mecânicas podem ser recomendadas para áreas menores ou para produtores com menor condição financeira.
De qualquer modo, ambas são soluções viáveis, principalmente quando apresentam boas práticas de uso, como manutenção atualizada, regulagem apropriada e operação criteriosa.
>>Leia mais:
“Moderfrota: veja o que é preciso para conseguir recursos“
“Regulagem de semeadora: 5 dicas para melhorar seu desempenho”
“Depreciação de máquinas: todos os cálculos de forma prática”
Restou alguma dúvida sobre semeadora mecânica e pneumática? Qual você utiliza em sua fazenda hoje? Adoraria ler seu comentário!